Galvanised steel is represented by cold- and hot-rolled coils with a zinc coating, which helps to protect the steel against atmospheric corrosion. Galvanised steel coils are successfully used in industries with stringent requirements for corrosion resistance, durability, strength and appearance, and can be formed or have various coatings applied. The key standards to be followed for the production of galvanised coils include EN 10346 (Europe), ASTM A653 / A653M (US), DSTU EN 10346 (Ukraine), GOST 14918−80 (Russia and the CIS) and GOST R 52246−04 (Russia). Manufacturers also have their own original standards.
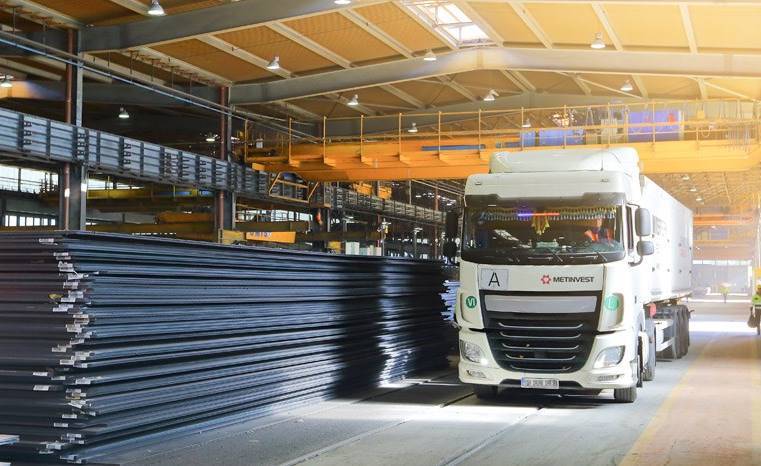
Application of galvanised steel coils
Galvanised steel coils are widely used in the following industries:
-
In the construction industry: to manufacture structural elements low-rise construction, light steel thin-walled structures, sandwich panels, lining of heat pipelines and various heat insulation, conditioning systems, metal roof shingle, profiled sheeting, culvert pipes, cladding of entry doors, elevators, reinforcement profiles for PVC windows and plastic doors, European-type fasteners for plasterboards, etc
-
In the automotive industry: to manufacture external and internal car body parts, as well as to repair external public transport body parts, eg for buses and trams)
-
In the machine building and instrumentation industries: to manufacture cases for electrical and mechanical equipment, home appliances, metering devices and packing
-
To manufacture houseware (tableware, bowls, buckets, tanks, baths, etc)
-
To manufacture colour-coated (and other type of coating) rolled steel
Technical pamphlets
-
Technical pamphlets
-
DX51D and DX52D hot-dip galvanized coils for cold forminglearn moreContinuously galvanized structural coils of S220GD - S350GD steel-gradeslearn more
-
Hdg coil classification, product range and properties
Standards applied in different countries to set the requirements for galvanized steel coils specify steel grade and size ranges for these products. Galvanised steel coils are classified based on the following features:
-
Application of coated steel (profiling, cold forming, manufacture of steel structures)
-
Chemical composition of coating material (pure zinc, zinc-iron/zinc-aluminium/aluminium-zinc/zinc-magnesium alloys, etc)
-
Thickness/weight of protective coating
HDG coils according to European and Ukrainian standards
Galvanised steel coils as per the European EN 10346 and the similar Ukrainian DSTU EN 10346 standards can be coated with zinc, zinc-iron alloy, zinc-aluminium alloy, aluminium-zinc alloy or aluminium-silicon alloy:
-
Zinc coating (Z) is achieved by dipping the prepared strip into a bath with molten alloy, containing at least 99% zinc. This is the most common and traditional way of protecting rolled steel from corrosion.
-
Zinc-iron coating (ZF) is formed by dipping a strip into a bath of molten zinc (at least 99% zinc) with further annealing to form a zinc-iron coating with an Fe content of 8-12%. Such coating is stronger than the traditional zinc coating and has better adhesion with substrate steel due to mutual diffusion between the iron and zinc in the surface layers. That is why this coating is less exposed to lamination or pitting under impact, mechanical stresses or deformation of treated products.
-
Zinc-aluminium coating (ZA) is applied to rolled steel by dipping it into a bath of zinc and about 5% aluminium with a minor content of mishmetal (mix of metals). Rolled steel with such coating has better formability and corrosion protection properties compared with zinc-coated steel.
-
Aluminium-zinc coating (AZ) is applied by dipping steel into a bath of molten metal consisting of 55% aluminium and 1.6% silicon (with the remaining being taken up by zinc). The combined action of these metals ensures the best corrosion protection compared with other coatings.
-
Aluminium-silicon coating (AS) is created by dipping steel into a bath of molten metal containing aluminium and 8-11% silicon. Galvanized steel coil with such coating is highly resistant to oxidation at high temperature (up to 650°C) and highly resistant to chemical corrosion.
Galvanised steel coils manufactured according to the EN 10346 and DSTU EN 10346 standards can be made from the following steels:
-
Low-carbon steel for cold forming (DX51D – DX57D). These products are classified based on suitability for cold forming: DX51D – bending and profiling quality; DX52D – drawing quality; DX53D – deep-drawing quality; DX54D – special deep-drawing quality; DX55D – special deep-drawing quality (only +AS); DX56D – extra deep drawing quality; DX57D – super deep drawing quality.
-
Steel for construction and framing (S220GD – S550GD). Rolled products are arranged in increasing yield stress (Rp0.2), which is indicated in the marking. Rolled products of S220GD – S550GD steel are mainly used in the manufacture of formed sections (Z-, C-, sigma-, U-shaped profiles, etc) for light-gauge steel structures.
-
Steel with high yield strength for cold forming (HX160YD, HX180YD, HX180BD, HX220YD, HX300LAD, etc). Such rolled products are arranged in increasing yield stress (Rp0.2), which is indicated in the marking. The marking also contains the following information: H – high-strength flat rolled products for cold forming; Х – as-rolled condition (hot-rolled or cold-rolled) is not defined; D – designed for hot-dip coating; B – heat-treated steel; Y – steel with higher formability; LA – low-alloy / micro-alloy steel.
-
Cold-formable multi-phase steel (HDT450F, HCT490X, HDT590X, HCT780X, HCT980X, HCT780T, HDT580X, etc). Rolled products are arranged in increasing minimum tensile strength (Rm0.2), which is indicated in the marking. The marking also contains the following information: H – high-strength flat-rolled products for cold forming; С – cold-rolled products; D – hot-rolled products; Т (nnn) – the minimum tensile strength in MPa. The last symbol: F – ferrite-bainite, Х – dual-phase; Т – TRIP, С – complex-phase; М – martensite.
Galvanised coils as per the EN 10346 standard can be coated with zinc, zinc-iron alloy, zinc-aluminium alloy, aluminium-zinc alloy or aluminium-silicon alloy. The coating weight is expressed as grams per square metre and characterises the weight of the coating deposited on the both strip surfaces. The coating type (Z, ZF, ZA, AZ, AS) and nominal weight are indicated in the coating designation. Depending on the type of protective layer, the minimum weight of coating on both surfaces of a galvanized product can be 100-600 g/m2 (average value for three spots).
Coating designation |
Minimum total coating weight for both surfaces, g/m2 |
Theoretical recommended values of the coating thickness per unit of surface for single-spot tests, microns |
Density, g/cm3 |
||
Three-spot |
Single-spot |
Reference value |
Interval |
||
Z100 |
100 |
85 |
7 |
5-12 |
7.1 |
Z140 |
140 |
120 |
10 |
7-15 |
|
Z200 |
200 |
170 |
14 |
10-20 |
|
Z225 |
225 |
195 |
16 |
11-22 |
|
Z275 |
275 |
235 |
20 |
15-27 |
|
Z350 |
350 |
300 |
25 |
19-33 |
|
Z450 |
450 |
385 |
32 |
24-42 |
|
Z600 |
600 |
510 |
42 |
32-55 |
Galvanised steel coils as per the EN 10346 and DSTU EN 10346 standards are also classified based on:
-
Types of surface quality:
-
А – surface quality right after coating application
-
В – surface quality improved by processing in a skin pass mill
-
С – highest surface quality also obtained by processing in a skin pass mill; the controlled surface should allow for the application of a homogeneous layer of decorative paint, while the other surface should have minimum quality B
-
-
Surface treatment:
-
Chemically passivated – С
-
Oiled – О
-
Passivated and oiled – СО
-
Phosphate treated – Р
-
Coated with organic insulation – S
-
-
Surface finishing:
-
Standard spangle pattern (normal gloss) N is obtained by allowing zinc coating to harden naturally
-
Minimum spangle pattern (minimum gloss) M is obtained by adjusting molten zinc composition and special measures for hardening and/or subsequent surface finishing
-
Geometry and size tolerances for steel sheets and strip coated by hot dipping should meet the requirements of the European EN 10143 standard and its Ukrainian analogue DSTU EN 10143.
HDG coils according to US standards
The main US standard followed for the production of hot-dip galvanized coils with metallic coating is ASTM A653/A653M.
Galvanised products can be produced from the following steels:
-
Commercial steel (CS, types А, В and С)
-
Formable steel (FS, types А and В)
-
Deep drawn steel (DDS)
-
Structural steel (SS)
-
High-strength low-alloy steel (HSLAS, types А and В)
-
Solution hardened steel (SHS)
-
Bake hardenable steel (BHS)
Depending on the class of selected zinc coating (G01-G360 for British Imperial system, or Z001-Z1100 for international system of units SI), the minimum weight of protective material can vary from 90 tо 1,100 g/m2 on both sides of the product.
Geometry and size tolerance for galvanised steel coils produced to ASTM A653/A653M should meet the requirements of ASTM A924/A924M.
HDG coils according to CIS standards
The key standards defining technical specification for zinc-coated steel produced in the CIS include GOST 14918 and GOST R 52246.
GOST 14918 is applied to cold-rolled hot-dip galvanised steel sheets and coils produced by continuous galvanising lines and intended for cold profiling, colour coating, manufacture of formed goods, tableware, tare and other metal goods. According to this reference document, steel can be classified based on:
-
Application: cold stamping, cold profiling, colour coating (skin passed), general application
-
Drawing capability: normal drawn, deep drawn, extra deep drawn
-
Smoothness of zinc coating thickness: normal crown, lesser crown
-
Spangle pattern: with spangle pattern, without spangle pattern
-
Class of coating thickness: enhanced (570-855 g/m2 on both sides); 1 (258-570 g/m2); 2 (142.5-258 g/m2)
Galvanised steel produced to GOST 14918 has a thickness of 0.5-2.5 mm and a width of 710-1,800 mm. Dimensions, acceptable tolerances and other requirements for the product range should correspond to GOST 19904.
GOST R 52246 is followed to produce galvanised steel coils with zinc and iron-zinc coating from low-carbon steel intended for the manufacture of goods by bending and interlocking joint as well as profiled, formed and welded metal ware. Galvanised rolled steel is classified based on:
-
Application:
-
01 – manufacture of flat and flat bent goods
-
02 – houseware, manufacture of goods by bending and interlocking joint
-
03 – formed extra deep drawn parts and complicated profiles
-
04 – formed complex drawn goods
-
05 – formed super complex drawn goods
-
06 – super deep drawn goods
-
220, 250, 280, 320, 350 – for profiled goods
-
-
Manufacturing accuracy:
-
Normal accuracy
-
Improved accuracy
-
High accuracy
-
-
Edge condition:
-
Mill edge
-
Trimmed edge
-
-
Weight of zinc coating – 60, 80, 100, 140, 180, 200, 225, 275, 350, 450, 600 classes
-
Zinc spangle pattern and surface finish:
-
Normal spangle
-
Normal spangle (skin-passed)
-
Minimum spangle
-
Minimum spangle skin-passed
-
Iron-zinc
-
Iron-zinc skin-passed
-
-
Surface preservation:
- Passivated
-
Oiled
-
Passivated and oiled
Galvanised steel produced to GOST 52246 has a thickness of 0.3-4.5 mm and a width of 700-1,800 mm when manufactured in sheets, or a width of 500-1,800 mm when manufactured in coils. Dimensions, acceptable tolerances and other requirements for the product range should correspond to GOST 19903 or GOST 19904.
Production of galvanised steel coils
There are two widely used methods for applying zinc coating on steel coils:
-
Hot-dip galvanising (HDG) technology is used to create a protective layer by immersing a steel strip into a bath of molten zinc. Hot-dip galvanised steel coils can be produced by continuous galvanising lines with non-oxidising annealing furnaces (the Sendzimir method and its variations) or by applying wet or dry flux (the Cook-Norteman method and its modifications). Hot- or cold-rolled non-annealed (full-hard) steel coils are used as feedstock for continuous hot-dip galvanising lines with non-oxidising annealing furnaces. The production process involves electrochemically cleaning, drying and annealing the strip to obtain the required mechanical properties, followed by immersing the material into a bath of molten zinc and controlling zinc thickness. The strip then undergoes forced cooling and finishing (passivation, oiling, levelling, drying and coiling the galvanized coil). When using lines that apply wet or dry flux, feedstock (before it is galvanized) should have the required set of mechanical properties since such lines do not have annealing furnaces. The strip is first degreased with an alkali solution and pickled in acid, following which a smooth layer of flux composed of a combination of zinc chloride, ammonia chloride and various additives is applied to the strip. The strip is then put into a strand furnace with a protective atmosphere, where the flux is dried, and is immersed into a bath of molten zinc. The flux completely removes residual pickling substances and moisture from the metal surface, and the thin film reduces the surface tension of zinc and ensures the best moistening of the metal surface. Hot-dip galvanising technology is fairly universal and is widely used in construction, machine building and other industries. It is used by both large steel mills and re-rollers/coaters.
-
Electrolytic galvanising is an electro-chemical process in which a layer of zinc is applied in a bath of acid or alkali electrolytes. The main idea of this technology is to use oxidising and reducing reactions, during which electrons move through the electron transport chain, while zinc ions in the electrolyte flow from anode to cathode. This type of coating is usually used for thin-gauge material; the coating thickness is normally 5-12 μm and it accurately follows the shape of the product. The absence of intermediate brittle layers makes electrolytic zinc coating more plastic compared with coating applied via hot-dip galvanizing. Major application areas for such products include automotive, transport and machine building, among others.
Buy galvanised steel coils from the manufacturer
Metinvest offers galvanised steel coils with a thickness of 0.4-2.0 mm and a width of up to 1,250 mm for construction and machine building applications. Products are supplied in accordance with the requirements of key international standards (EN 10346, ASTM A653/A653M, GOST 14918, GOST R 52246). Galvanized steel coils can be purchased through the Group’s global sales network of 38 sales offices in Europe, Asia, Africa and North America, as well as 16 metal service centres in Ukraine and authorised dealers.
Get in touch
Find the nearest office
Subscribe to our newsletter