Pig iron is a multicomponent iron alloy containing carbon (> 2.14%) and other elements. It is most widely used in steelmaking due to its balanced process and performance parameters.
Steel is a type of metallurgical metal product containing carbon (from 0.025% to 2.14%), impurities and alloys. It is an essential component in machinery and instrument engineering, construction and other industries.
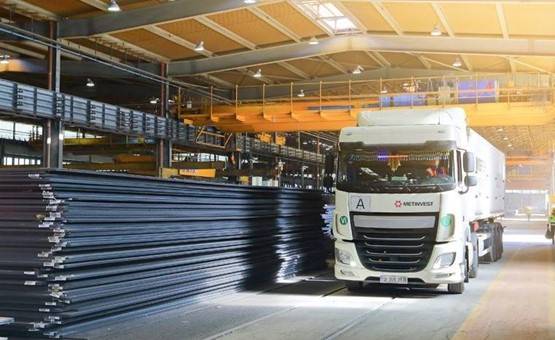
Basic chemical composition
Grade of pig iron* |
Elements, % by mass |
||||
C |
Mn max |
Si max |
S max |
P max |
|
P1 / P2 / PL1 / PL2 |
3.5-5.0 |
1.00 |
1.20 (target 1.00) |
0.05 |
0.10 (target 0.08) |
*Pig iron supply is also possible under customers' technical requirements.
Production of pig iron and steel semis
Iron is produced in a blast (shaft) furnace, which is a vertical structure with refractory lining and steel shell up to 35 mm thick. The blast furnace process involves reducing iron (from iron ore) when it reacts with carbon oxide, hydrogen and solid carbon, which are released during fuel combustion in the furnace.
Iron ore materials, fuel (coke) and flux (limestone, burnt lime) are charged into the top of the blast furnace in the required quantity to produce hot metal; while air enriched with oxygen, natural gas, steam, etc, are blown into the bottom. Combustion takes place and the heated burden descends. As a result, hot metal containing 4.0-4.3% of carbon is produced.
The steelmaking process consists of such steps as charge material preparation, melting, secondary metallurgy and casting. Raw materials include hot metal or pig iron, scrap steel or iron, and ferroalloys. The most important is to remove excessive carbon, silicon, manganese and other impurities from the hot metal. Key steel production methods include basic oxygen, electric arc or open hearth furnaces.
The basic oxygen approach is now widely used to make steel in a basic oxygen furnace using hot metal. Charge materials include hot metal, scrap metal and mould powders (lime, fluorspar, iron ore and bauxite).
The electric arc furnace method is widely used to make high alloy, structural and special steels and alloys. Melting furnaces are classified into arc and induction types.
The open hearth furnace approach is used less and less due to its low production efficiency and environmental impact. The process takes place in the hearth of a reverberatory furnace.
Whichever route is used, the tapped steel is subject to ladle treatment to achieve the required chemistry and temperature. In doing so, steelmaking and casting become more cost-efficient. Units used for preheating, stirring and refining steel and adjusting chemical composition are called ladle furnaces.
Casting is the final step in steelmaking to produce solidified strands for further processing at hot-rolling mills. Nowadays, the main approach is continuous casting, which accounts for about 95% of all steel, while the remainder is teemed into ingots.
Continuous casting machines (casters) produce such semis as square billets or blooms for making sections and structural; slabs with rectangular cross-sections for manufacturing plates (sheets); round or hollow billets for pipe-making; and beam blanks for making wide flange beams. The solidified material from a caster can be fed directly to a hot-rolling mill, whereas ingots require further hot-rolling to be converted into semi-finished products.
Iron and steel classification
Iron is classified into:
Pig iron / hot metal (for steelmaking)
-
Cast iron (for castings intended for various applications)
-
Special iron (such as specular pig iron, ferroalloys)
Iron is also classified by the following criteria:
-
Position in the Fe-C phase diagram against the eutectic point: hypoeutectic, eutectic and hypereutectic iron
-
Carbon state and form in the material structure: grey, white, mottled, chilled, malleable, ductile and compacted graphite iron
-
Metal base structure: pearlite-cementite, pearlite, ferrite-pearlite and ferrite
-
Chemical composition: non-alloy and alloy
-
Performance properties: structural and special iron (ornamental iron, anti-friction and wear-resistant iron, heat-resistant iron, corrosion-resistant iron, iron with special magnetic properties, etc)
For supply purposes, shape, size, weight and chemical composition are marked on commercial pig iron.
As per national standards and industrial statistics, steel is classified by several criteria, the main ones of which include:
-
Production route: OHF, BOF and EAF steel
-
Chemical composition: carbon non-alloy and alloy steel
-
Quality: standard-quality, quality, high-quality and superior-quality steel
-
Equilibrium structure: hypoeutectoid, eutectoid, hypereutectoid
-
Structure after air cooling: bainite, ferrite, pearlite, martensite, austenite and ledeburite; there may be mixed structures, e.g. ferrite-pearlite
-
Main properties and application: steels for general application, structural steel, instrumental steel with special properties (stainless, heat-resistant, fire-resistant and wear-resistant steel, etc).
When delivering semi-finished steel products (slabs, blooms, and billets), chemical composition, geometry, dimension tolerances, surface quality parameters, macrostructure, microstructure, etc, are all governed.
Buy pig iron and slabs from the manufacturer
Metinvest is one of the largest global suppliers of pig iron and steel slabs. These semi-finished goods are produced by the Group’s integrated steelmakers in Ukraine and can be purchased through the global sales network of 38 sales offices in Europe, Asia, Africa and America.
Producer |
Thickness, mm |
Width, mm | Steel grade standards | |||
PJSC Azovstal Iron and Steel Works |
220-300 |
1250-2100 |
DSTU/GOST/EN/ASTM/ Customer's technical requirements
|
|||
PJSC Ilyich Steel |
150-250 |
1000-1900 |
Get in touch
Find the nearest office
Subscribe to our newsletter