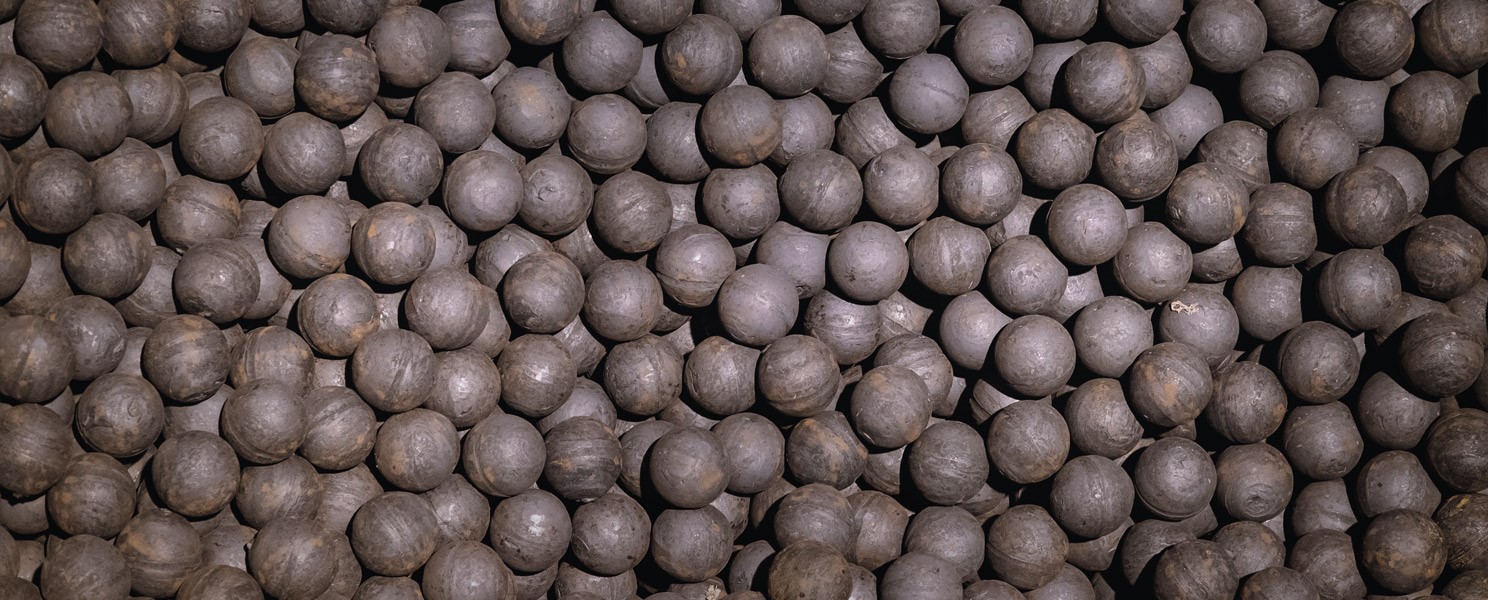
Grinding balls are used in the mining, coal, construction (for example, to make cement) and other industries: in ball mills as grinding bodies for grinding materials by impact, abrasion and crushing. The balls are produced from iron and steel.
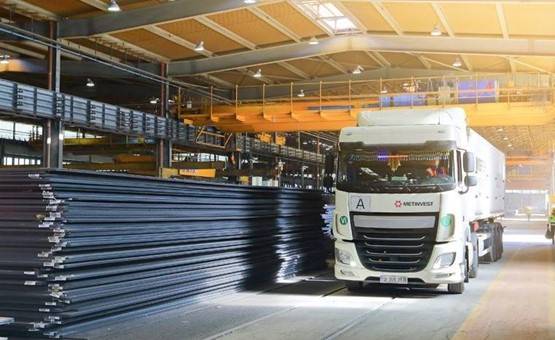
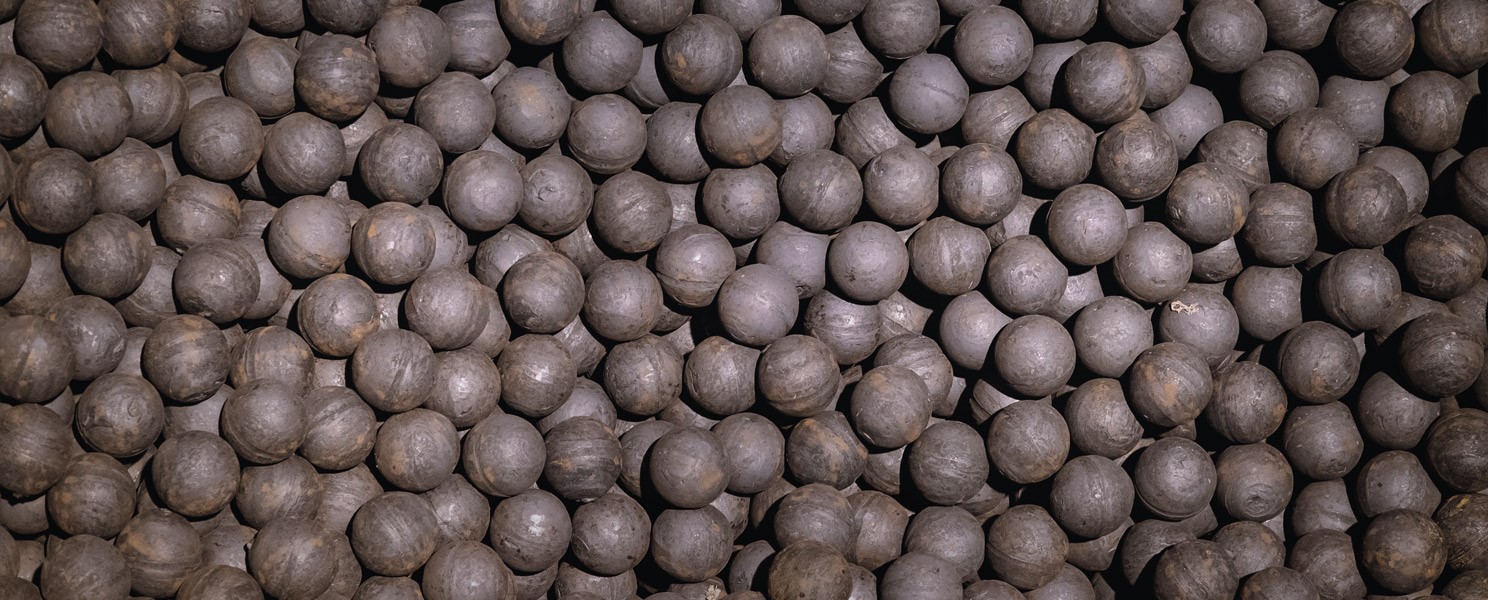
Downloads
-
Catalogue
-
Long productslearn more
-
Application
A drum mill is a device where the materials are crushed by a cylindrical or cylinder-conical drum, half of which is filled with grinding media, while the drum rotates around its horizontal axis. As a rule, the feedstock is loaded on one side of the unit, and the crushed product is unloaded on the other. When the drum rotates, the grinding media grind the material in free motion, i.e. reduce the size of its particles by mechanical impact. The grinding media are iron and steel balls for a ball mill with a diameter of 15-150 mm; carbide balls with a diameter of 8-20 mm; iron or steel cylinders (such as "cylpebs"); round steel rods with a diameter of up to 130 mm and a length corresponding to the length of the mill drum; and silicon or ore pebbles up to 200 mm in size, large pieces of crushed raw material. As such, there are ball, rod, pebble, ore-pebble and autogenous mills.
To increase the resistance of the inner walls of the drums, they are lined with plates of steel casting or rubber, plates of hard alloys and other materials. Drum mills are used in metallurgy and mining: in the enrichment of extracted raw materials, for the preparation of pulverised coal, etc. Depending on the technology chosen, drum mills are divided into units for dry and wet grinding. To ensure the required size of the crushed raw materials, the equipment is combined with classifiers (air separators, hydrocyclones, etc.), which divide the material obtained in the mill into fine and coarse. Fine product is processed further, while the coarse one is returned to the mill for additional grinding.
A ball mill is a drum-grinding unit where balls from solid materials (steel, iron, hard alloys, ceramics, etc) are used. Most common are ball mills, where when the drum rotates and the balls rub against the inner walls, the balls are lifted until the lifting angle becomes bigger than the angle of repose. Then the grinding media are again below. The material is ground by abrasion between the inner surface of the drum and the ball, as well as between the balls themselves. The impact of the balls when they fall crush the material.
One type of ball mill is a planetary mill, in which several vertical drums (usually from 3 to 6) are placed on a disk and rotate around their axes, and all together: around the axis of the disk. The opposite direction of rotation of the drums and disk causes the grinding media to roll and rotate, creating intensive grinding.
Classification and properties
Steel grinding balls for ball mills can be manufactured according to both international and national standards (e.g., DSTU 8538, GOST 7524) and according to specifications of manufacturers and consumers. The main features and classifiers are:
- Product material: iron, steel, carbide material, ceramics
- Production technology: centrifugal casting, hot-rolling, casting, stamping, sintering
- Ball diameter: mm
- Hardness: normal, higher, high
The most common are grinding balls of carbon and low alloy steels, used primarily for grinding raw materials. Such grinding media for ball mills are produced by hot-rolling, forging and stamping. Balls are hardened by microalloying steel and heat treatment.
The technology for producing iron balls is more complicated (centrifugal casting); they are used primarily for grinding cement and non-ferrous metal ores. The wear resistance of such products is increased by alloying cast iron with chromium, vanadium, molybdenum and nickel.
The main quality parameters of steel grinding balls manufactured according to DSTU 8538 are: rated diameter, nominal diameter, maximum deviations of diameter and hardness. The rated diameter is the diameter of the ball, rounded to the nearest values of the standard series. The nominal diameter is the diameter against which the limit deviations are determined. Maximum deviations are the difference between the limit and nominal diameters.
Rated diameter, mm |
Nominal diameter, mm |
Maximum deviations from the nominal diameter, mm |
15 20 25 |
15,0 20,0 25,0 |
±1,0 |
30 35 40 45 |
31,5 36,5 41,5 46,5 |
±2,0 |
50 55 60 65 70 80 |
52,0 57,0 62,0 68,0 73,0 83,0 |
±3,0 |
90 100 |
94,0 104,0 |
±4,0 |
110 120 |
114,0 125,0 |
±5,0 |
According to DSTU 8538, the hardness of balls after heat treatment shall comply with the standards for the corresponding group specified.
Rated ball diameter, mm |
Hardness group |
||||||
1 |
2 |
3 |
4 |
5 |
|||
HRC/HB hardness, min |
|||||||
Ball surface |
At 0.5 depth of the radius |
Ball surface |
Bulk |
||||
From 15 to 45 |
45/415 |
49/461 |
55/534 |
55/534 |
45/415 |
61/601 |
57/555 |
From 50 to 70 |
43/401 |
48/453 |
53/514 |
53/514 |
43/401 |
60/590 |
53/514 |
From 80 to 100 |
39/341 |
42/375 |
52/495 |
52/495 |
40/352 |
58/567 |
48/453 |
From 110 to 120 |
35/302 |
38/331 |
50/477 |
50/477 |
35/302 |
56/545 |
43/401 |
Volumetric hardness is a calculated indicator of hardness, based on the volume of a steel grinding ball.
Production
The most common technology for producing steel grinding balls is hot-rolling. Cross-rolling is used when the initial round billet, after heating in the furnace to a predetermined temperature, is fed to a ball rolling mill, where it is reduced in rolls with screw gauges rotating in the same direction. A schedule of two or three rolls can be used. When leaving the rolling stand, the grinding media are cooled with water or a water-air mixture to increase strength properties, with further self-tempering in the bins.
An alternative method for producing grinding balls from steel is stamping, but it is less common due to lower line productivity (two to three times) and higher metal consumption (10-20% more).
Purchase
Metinvest offers grinding balls for ball mills with diameters from 30 to 120 mm of 1-4 hardness groups for the mining, coal, construction (cement manufacturing) and other industries. Steel balls can be purchased through the global sales network of 38 sales offices in Europe, Asia, Africa and America, as well as 16 metal centres in Ukraine, and authorised dealers
Get in touch
Find the nearest office
Subscribe to our newsletter