The great war has led to one of the biggest crises in the construction industry since Ukraine's independence. On the one hand, millions of square metres of residential and other real estate have been destroyed or damaged, and the scale of destruction is increasing every day. On the other hand, construction volumes have declined significantly, down 65% as of the end of 2022.
And even after the hostilities are over, we should not count on rapid growth unless there is a change in approach. Construction market players are already facing a labour shortage. When the volume of construction increases, the crisis will become even more pronounced.
Aside from addressing the labour shortage issue, it is time to think about how to make construction less labour-intensive. One possible option is to use off-the-shelf solutions. Prefab (use of prefabricated large components in construction) and modular construction technologies are widely used around the world. They are especially advantageous in regions that have suffered from natural disasters or war, like Ukraine.
Such solutions significantly speed up the rebuild process while making it cheaper and require fewer skilled labour.
Prefab is a method of construction that uses elements or parts of a building made off-site in a factory.
Rethinking рrefab: does speed meet quality?
Not the most successful, but effective example of mass fast construction based on standard designs at the time was 'khrushchyovkas' – five-storey panel or brick buildings without elevators which began to be built en masse during the post-war period in the 1950s.
The idea was by no means new - modular housing construction after the Second World War was widespread in Germany, where a system of building housing from prefabricated elements, known as 'Plattenbau', was developed.
In France, the post-war modular reinforced concrete buildings in the downtown of Le Havre, designed by Auguste Perret, were even declared a UNESCO World Heritage Site.
But Soviet 'khrushchyovkas', like most ideas that were borrowed from abroad and re-imaged at the time, became rather a negative example that created the perception that fast modular construction always has a negative impact on quality.
After all, 'khrushchyovkas' were built not only without exterior frills, but also without heat and sound insulation, with not very good layouts - cramped rooms and not always made of high-quality materials. Such housing was designed for 30-50 years of operation, so now a lot of such buildings are simply falling apart.
Construction technologies, meanwhile, have come a long way, and there are examples of high-quality modular construction made of modern materials with good planning and design.
While the Ukrainian market mainly uses this technology to build small individual residential buildings, it is common to use prefabricated structures for multi-storey applications around the world.
For example, in 2022, the Netherlands completed the construction of the De Zalmhaven skyscraper of over 200 metres in height which was built on the basis of prefab solutions using precast concrete, sandwich panels, and facade finishes made in-house.
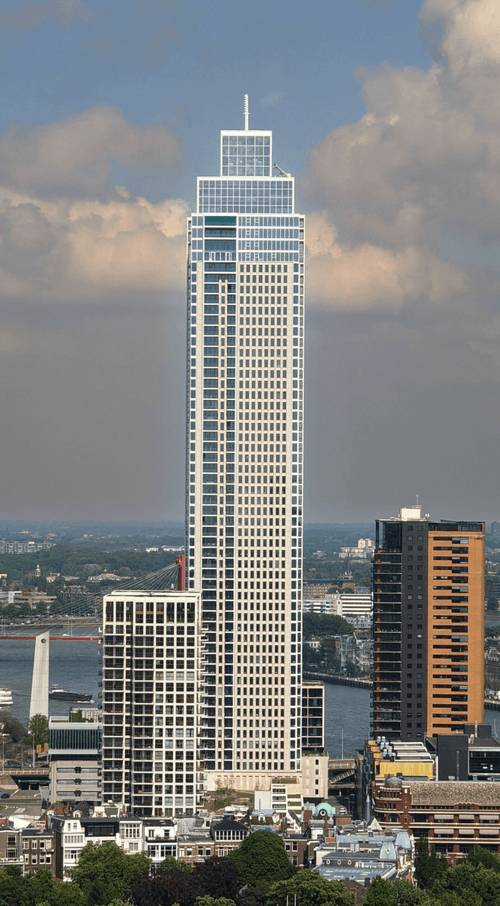
De Zalmhaven
Precast structures were manufactured in a special closed hangar next to the building with special temperature conditions. Thanks to this, the team completed one floor of the building every week. Due to the speed and height of the project, the construction process was called a "flying factory".
"Ready-made modular elements speed up the cycle on site. This is perhaps their most important advantage. Another significant benefit is the reduction in labour involved in construction. However, it is important to bear in mind that, in addition to the construction of buildings, the modules manufacturing cycle and their installation should be factored in," says Volodymyr Sementsov, co-founder and managing partner of INSPI Development.
Metal or reinforced concrete
Most examples of modular housing development in the last century are associated with reinforced concrete. Nowadays, the use of prefabricated modular metal structures is popular around the globe.
Metal has many advantages - it is lightweight, durable, and strong, allowing to bring the most daring architectural forms to life. Not to mention, metal is almost 100% recyclable and is considered a more environmentally friendly building material than concrete. And most importantly, it is a faster way to build, because reinforced concrete structures take time to reach their design strength even in a factory environment. Metal, on the other hand, can be worked with right after it is produced.
The disadvantages of metal, such as corrosion or high thermal conductivity, can be addressed by using special coatings and modern insulation materials.
Prefabricated steel structures can be used to build industrial facilities, as well as residential or office buildings and social infrastructure. Such construction is possible in almost any weather conditions and even in winter.
Modular steel buildings hold the world records for the speed of construction of high-rise buildings. For example, a 30-storey hotel was built in China in 15 days. And with all utilities, exterior and interior outfitting, and even furniture.
The Chinese built a 57-storey skyscraper with 800 apartments in 19 days using prefabricated metal platforms. Thanks to this technology, the builders managed to erect and outfit 3 floors per day.
In addition to speed, one of the benefits of prefabricated steel construction is cost-effectiveness. The cost of materials is usually the same as in conventional construction, but savings are achieved through faster construction and fewer workers on site. This means lower labour costs, expenditure on rental of machinery and equipment, etc.
The construction of the same 30-storey hotel in China required about 200 builders and only one tower crane and a few trucks to transport the finished structures.
It is clear that the endeavours of the Chinese to meet such construction deadlines were primarily fuelled by the desire to set a record, so the work continued around the clock. But even under normal conditions, with the time required to manufacture modular structures in mind, such construction is much faster.
For example, an eight-storey metal-framed building designed by Ukrainian architects for the project "Steel Dream" can be erected in just nine months, while reinforced concrete construction can take 2-3 years. According to the designers' calculations, a kindergarten can be built twice as fast as using conventional construction methods.
Metal buildings weigh 3-4 times less than those made of reinforced concrete or brick. This reduces the cost of foundation work and saves up to 30% of the cost.
Modular structures are suitable for both brownfield development, as they do not require a large construction site, and for greenfield construction, as the Chinese often like to do.
The downsides of modular construction are the limitations of planning solutions due to transport dimensions and more expensive logistics.
All in all, the demand for such construction is growing around the world. The size of the modular and prefabricated construction market surpassed USD 147 billion in 2022 and is expected to reach capitalisation of USD 285 billion by 2032, growing at an average annual rate of 7.85%.
Prefab solutions in Ukraine
Most Ukrainian companies engaged in modular construction specialise in the construction of individual one- or two-storey housing. Such decisions are unlikely to come in handy in the reconstruction of cities and towns destroyed by the fighting.
Rinat Akhmetov's Metinvest was one of the first companies to propose the concept of rebuilding multi-storey housing and social infrastructure facilities using prefabricated steel structures.
Experts developed 13 designs of steel buildings up to eight storeys in height. In total, taking into account various versions of design, layout and number of storeys, there are more than 200 ready-made designs based on three prefabricated steel elements (prefab solutions) - a frame, a module, and a platform.
The concept includes residential development (high-rise buildings up to 8 storeys in height, a dormitory, and a hotel), social infrastructure facilities (a school, kindergarten, and outpatient clinic), as well as leisure and engineering facilities (a car park, sports complex, and underground shelter).
15 Ukrainian fabricators of steel structures expressed their readiness to join the project at the conceptual stage. This is another positive trend, as the funds that will be channelled to Ukraine to finance the reconstruction will be directed to the strengthening of the Ukrainian economy, and all the added value will remain here.
It is important that the designs with bills of quantities that need to be adapted to fit the location have already been developed, so construction can begin.
Of course, rapid construction should not turn cities into reinforced concrete ghettos. In this regard, it is necessary to draw on the expertise of urbanists and other specialists, as housing and social infrastructure facilities are only part of the reconstruction concept. Long-term construction projects are simply not an option for Ukrainians in the wake of the war, because otherwise funding given to Ukraine for its reconstruction will quickly run out.
"Today any new forms of construction or experimental solutions should be supported, because this is the way forward. The main thing is to follow the principle of "let's rebuild better", look for new opportunities and test their effectiveness. But in this case, the role of urbanists, architects, and planners increases significantly. Everyone knows that home is more than just a house, it is the space we live in. Aside from practicality of a dwelling as a component of a building with its aesthetics, it needs parks, public gardens, and proper infrastructure. So, reconstruction using new technologies should be looked at in conjunction with the development planning," says Volodymyr Sementsov.
Many local communities, especially those heavily affected by shelling, will have the opportunity to completely redesign public spaces and built-up areas during the reconstruction process, relying on the latest global trends. Much of the visioning, discussion, and planning can and should be done now.